At one of the leading waste-to-energy plants in the world, at Gothenburg in Sweden, the cranes have been fitted with ICRAS anti-sway systems to increase productivity. 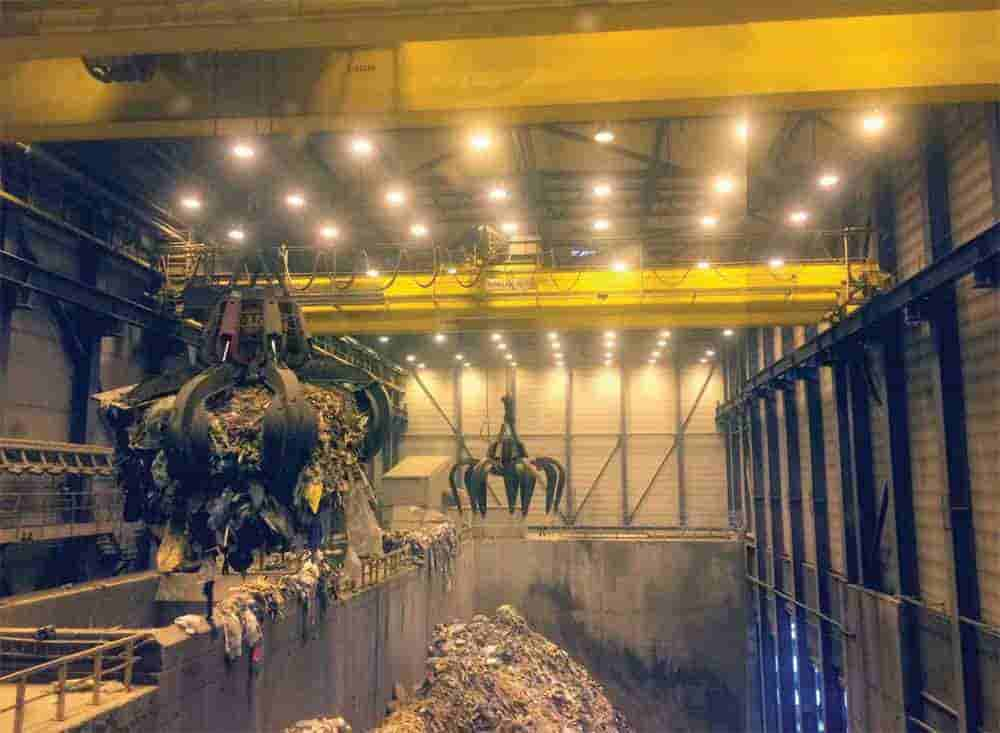
Waste-to-Energy (WtE) plants use incineration to burn waste—such as residual municipal solid waste (MSW), commercial, industrial and refuse-derived fuel—to power steam generators that make electric energy and heat to be used in homes, businesses, institutions and industries. The process can reduce waste by up to 90% and recover energy and raw materials. Modern WtE plants are clean and efficient—although some critics point out that part of the waste could be more environmentally recycled into raw material for new products instead. Each WtE plant has a storage pit bunker in which waste trucks deliver waste during daytime operations. In a typical arrangement, two high-capacity overhead cranes are used to mix and distribute waste inside the storage pit, and to feed incinerator hoppers when requested by the incinerator process computers. Waste pit cranes are specially-designed process duty cranes built to last through decades of continuous operation in aggressive environment, partly because waste pits are very unfriendly workplaces for maintenance operations. Crane travelling and hoist speeds are unusually high for overhead cranes, and the lifting height varies from 5–35m in normal operation. Waste storage cranes are fitted with grabs to pick waste, which in modern installations are electro-hydraulic, and cost around €100,000 each. While waste pits are not the most accommodating sites for crane maintenance staff, damage repair operations on waste grabs is even worse. Therefore, it is essential to design the process so that the grabs are not damaged by collisions against pit walls. While cranes typically operate near storage pit walls with 10–35m load pendulum length, even relatively small load sway can cause high impact forces which damage the grab hydraulics, mechanics, or control systems. Well-designed control systems that reduce stress and wear on crane mechanics and protect the waste grab from collisions can reduce WtE plant maintenance cost significantly, and prevent production breaks. WtE cranes are very demanding applications for sway control systems. Crane lifting speed is very high, and accurate positioning and collision avoidance must be performed while load height is changing rapidly. The cranes operate continuously near the waste pit walls, thus the sway control system must be able to react swiftly without reducing the cranes’ handling capacity. The system also has to be able to optimise short movements when the crane operates with long load pendulum lengths, where one period of load sway takes up to ten seconds. Renova Miljö AB’s waste-to-energy plant at Sävenäs in Gothenburg, Sweden is one of the world’s most advanced facilities for the boiling of waste to produce steam for heating and electricity. This plant has four boilers fed from one waste storage pit with two cranes. Around 150–200 trucks deliver waste to the plant daily. During daytime cranes are manually operated to avoid collisions with unloading waste trucks, but during nightshift unmanned operation using automation system is possible. While the cranes were originally fitted with inverter drives with an electrical load sway system built in, this system was not able to optimise crane movements as well as a human operator could. That resulted in significantly reduced feeding capacity in automated operation. Full power and heat production capacity was only achieved using crane drivers. When the SC-CP-V Sway control system from ICRAS Motion Control Solutions became available at the end of 2016, Renova was one of the first customers to place their order, with installation completed in March 2017. Connecting the SC-CP-V modules with the existing Siemens S7-400 automation system, and commissioning the sway control and collision avoidance systems took just a few hours, and after three days of crane automation cycle reprogramming the plant had reached the required production capacity increase. With the new sway control system in place, the cranes can operate faster than in operator-controlled mode. Renova Miljö project engineer Mikael Strand says, “Renova Miljö AB has been operating WtE cranes since 1972. After expansion of our plant 1994 and installation of the current overhead cranes we had problems with the capacity of our waste pit crane automation systems. Automated cycles were significantly slower than manual operator control. Therefore, automated operation was not possible while operating our plant with full capacity. “With the new load sway control and automated positioning system delivered by ICRAS Motion Control Systems our cranes’ automation cycles are significantly faster, and meet our performance requirements. Efficient use of hoist, trolley and bridge motions simultaneously reduces crane cycle times and gives us the materials handling capacity improvements we need to operate our plant with full capacity.” While many existing WtE plants like Renova have addressed crane capacity limitations by increasing crane transport capacity and efficiency, there is also another common problem, says Kimmo Hytönen, chief executive at ICRAS: “Many cranes’ electrical systems are at the end of their lifetime. ICRAS can provide sway control as an addon module that fits into practically any crane automation system. This makes the system very flexible, as the crane can be modernised using any inverter drive and automation supplier, without losing production capacity.” Swedish company KLAB modernises cranes using standard inverter drives instead of more costly crane OEM products. Sven Holmer, director of KLAB, says: “KLAB has replaced inverter drives on a one-to-one basis at Vattenfall WtE Uppsala in Sweden. The existing inverters had come to the end of their lifetime. KLAB also installed sway control from ICRAS Motion Control Solutions to replace the built-in sway control of the old drives. It was really easy to set up and adjust the sway control from ICRAS. This is always very important on site when the commissioning time is very limited, and site engineering time is very expensive.” The cranes have been fitted with ICRAS anti-sway systems to increase productivity.
|